In the molten salt electrolysis process and the metal thermal reduction process for the production of rare earth metals, due to the influence of impurities in the raw material, the container apparatus, an operating tool, atmosphere and other factors, a rare earth metal impurity content of the above two methods than prepared high. The purity is generally around 99%. With the rapid development of high-tech, many new rare earth functional materials have higher requirements for the purity of rare earth metals, which are greater than 99.9% or even 99.99%, and some limit the content of some non-rare earth impurities. In recent years, the application of high-purity rare earth metals has been continuously developed, such as high-purity lanthanum and cerium for Tb-Dy-Fe giant magnetostrictive materials, high-purity lanthanum, cerium and lanthanum for the preparation of magneto-optical targets, high purity é•, é’¬ , é“’ , é“¥ for high-efficiency metal halide lamps, high-purity bismuth, antimony for magnetic refrigeration materials. The development of rare earth metals to high purity has become one of the important topics in the research and development of rare earth metals.
The impurities in the rare earth metal can be classified into two types of rare earth impurities and non-rare earth impurities. Rare earth impurities refer to rare earth elements other than the main rare earth elements. The content of rare earth impurities indicates the degree of separation of rare earth elements. Although the existing purification method has a poor effect on removing rare earth impurities, rare earth impurities can be used. Low-purity rare earth oxides are used to prepare rare earth metals; non-rare earth impurities include metals other than rare earth elements, non-metallic impurities, especially impurities such as C, O, N, H, etc., which have low solubility in metals, mostly oxides and nitrogen. In the form of compounds, hydrides, etc., purification is difficult. At present, the purification methods of rare earth metals mainly include vacuum distillation, vacuum melting, molten salt extraction, electromigration, regional melting, electrolytic refining, and zone fusion-electromigration combined methods [1] . The purification of rare earth metals has the following characteristics: rare earth metals are active and easily interact with metal and non-metallic impurities. Therefore, purification should be carried out in argon or vacuum. At the same time, suitable crucibles and condensers should be selected to avoid contamination of rare earth metals. Any purification method has a poor effect on removing rare earth impurities in rare earth metals, so rare earth metals with as low a rare earth impurity as possible should be selected as the raw material to be purified; any purification method can only remove some of the rare earth metals. Impurities, so when selecting the purification method, it is necessary to comprehensively consider the type of impurities, purity requirements, purification effects, and if necessary, combine several methods to remove impurities.
references
1. Zhong Junhui, High Purification Technology of Rare Earth Metals [J], Rare Earth, 1992, 13(3): 44
Dust removal plays an important role in the treatment of air pollution. With the continuous development of industry, the quantity of particulate pollutants discharged is increasing, the concentration of dust in the atmosphere is increasing, and the dust is more and more harmful to people's living environment and human health. Higher requirements for the performance and reliability of dust removal equipment are put forward.
The traditional dust collector has been difficult to meet the requirements of high standard discharge and superior economic performance. The dust collector device is divided into mechanical dedusting device, electric dust precipitator, wet dedusting device and filter dust-removing device.
With the rapid development of energy and chemical industry and the deterioration of environment, a higher requirement for liquid cleanliness is put forward, and the petrochemical filtration device will be applied more widely in this field. The separation of solid impurity particles and the recovery of adsorbent and catalyst in gas phase and liquid phase in energy chemical industry. By filtering the solid impurity in the material to prevent the impurity particles entering into the device, the equipment, the pipe fittings are damaged or clogged, so as to ensure that the production medium meets the requirements of the process design and the normal and stable operation of the production device. Protect the safe operation and life cycle of the production plant.
The filter device can be divided into two types according to its structure: pipeline filter device and device filter device. It can be divided into: sulfur recovery and filtration unit (rich and poor liquid filter device, amine liquid filter unit, solvent collection filter unit,) hydrofining filter unit, hydrogen production filter unit, hydrocracking filter unit, catalytic filter unit and so on.
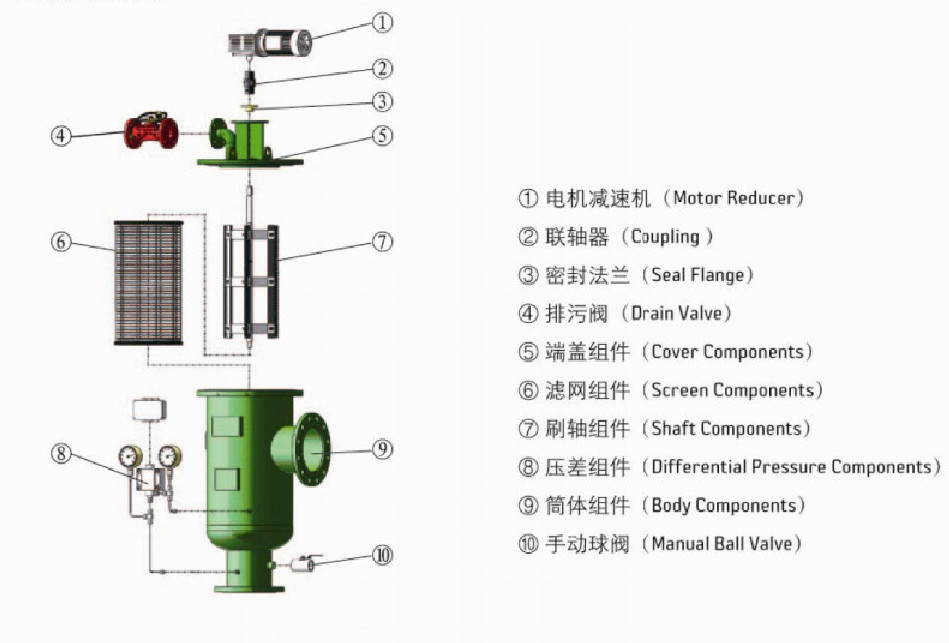
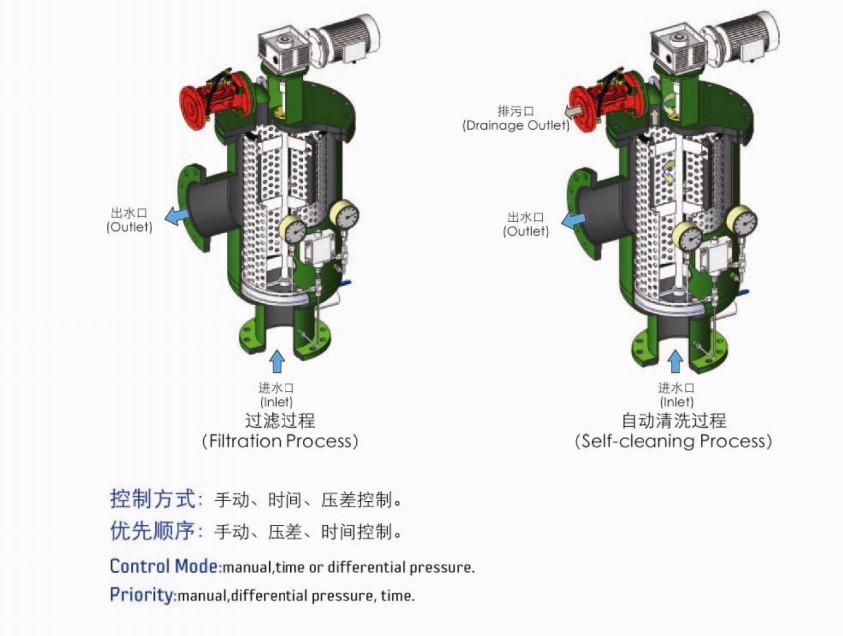
Filtrer Devices
Centrifugal Filter,Filtrer Devices,Device For Filtrer Replacement,Stainless Steel Filtrer Devices
Henan Sinofiltec Technology Co.,Ltd , https://www.airfilters.pl