From the 9th year of the Chinese invented the world's earliest caliper (new copper caliper), the caliper has been hailed as "the eyes of industry." Today, when the call for "artisan spirit" returns, calipers have become one of the indispensable precision measuring instruments in the modern manufacturing industry.
Xu Zhengwu, chairman of Dongguan Nano Titanium Measurement and Control Technology Co., Ltd. (hereinafter referred to as "Na Ti"), a liberal arts student, "half-way" has won the market opportunity. He established Natium in Dongguan Zhongtang last year and developed the world number one. A caliper automated assembly line. At present, the company produces 20,000 calipers per month, and it is estimated that the first year's output value will reach 25 million yuan. Xu Zhengwu said that it is estimated that after three years, the annual output value of the company will reach 10 billion yuan.
The world's first automated assembly line was put into production. In June last year, Xu Zhengwu officially registered NaTi Company in Dongguan. At the end of last year, the company established a research and development center and production base in Nanhuang Road, Zhongtang Town, Dongguan. It is worth mentioning that this new company that has just joined “Dongguan Manufacturing†has a “world first†new technology – the world's first automated assembly line for calipers.
Interestingly, before this, Xu Zhengwu was a liberal arts student who was passionate about psychology, training, and philosophical research. Entering the industry was based on curiosity about calipers.
After in-depth research, Xu Zhengwu discovered that although the caliper is known as the "eye of industry", it is valued by the world's advanced manufacturing countries such as the United States, Germany, Japan, etc. However, China is the world's largest caliper production country, the caliper made in China. It accounts for 75% of the global share. At present, China has an annual production capacity of about 30 million calipers and an annual output value of about 50 billion yuan. However, this type of measuring instrument, which is widely used in precision manufacturing, has not achieved breakthroughs in its production process over the past few decades.
In Xu Zhengwu's view, the annual production capacity of 30 million yuan can be described as a "sweet" for the big market. “I have visited Chinese and foreign companies. In Germany, almost every advanced manufacturing company has 5 calipers for a CNC machine tool. At present, most domestic enterprises have not implemented a machine tool with a caliper.†He believes that due to traditional craftsmanship The production capacity is not going up, the caliper cost is high, and the maintenance is not easy. The huge market demand in the past few decades has not been met.
"Until now, the production of calipers at home and abroad still employs artificial means, relying on the technical artisans to polish the steel, so the production efficiency is low, the cost is high, and the profit is low." Xu Zhengwu told reporters.
Business opportunities are often hidden in the "pain point" of the market. Due to the traditional craftsmanship, the caliper has been stuck in the manual production stage. As an indispensable part of the advanced manufacturing industry, it has been delayed in modern production. This is the “pain point†of the caliper manufacturing industry. Xu Zhengwu is determined to solve this "pain point" and realize the fully automated production of calipers.
Solve the "pain point" of modern production one by one
Before the establishment of Nano Titanium, Xu Zhengwu's team had spent 10 years researching the production process of calipers.
In his view, to achieve automated production, it is necessary to break the traditional process of “one-piece molding†of calipers, and to achieve precise quantitative production of various components of the caliper through “reconstruction to zeroâ€, and then integrate the various components through precise assembly technology. One. This process not only improves the production efficiency of the caliper, but also reduces the maintenance cost of the instrument.
However, the problem has come again. The caliper itself exists for accurate measurement. How does the caliper that is “assembled†ensure that the components fit together? After ten years of research and development, Xu Zhengwu and his team successfully overcome this technical problem, the birth of the "addition production" product structure patent, and finally achieve the precision "assembly" production of calipers.
In fact, Xu Zhengwu found and solved the industry's "pain point" is not only one. At present, Natati has a number of technical patents, each patent is a good way to treat "pain points".
The general gauge calipers are easily damaged by dust when used in the production hall due to the open rack. Moreover, the caliper is integrally formed, and the entire caliper is discarded once the component is damaged. Short life, this is another big "pain point" of the caliper. Nano Titanium has proposed a high-protection solution to this problem. With this patented technology, the rack is hidden in the caliper and has a good dustproof effect.
In addition, the general caliper jaw hardness is often between 40 and 50 degrees, the low hardness brings measurement error and service life problems. In response to this “pain pointâ€, Natto uses special materials to handle this process, achieving a hardness of up to 90 degrees, improving measurement accuracy and the life of the claws. These two technologies enable the calipers manufactured in Dongguan to reach five times the average life expectancy of the industry and can be customized.
Under the leadership of Xu Zhengwu, NaTi Company solved the “pain point†of modern production of calipers one by one. At present, NaTi has obtained a number of national patents, which has become the key to the entry of nano titanium calipers into the automated assembly line. Xu Zhengwu revealed that the company can produce 20,000 gauge calipers per month, and the estimated annual output value is 25 million yuan. In the next three years, the company will be able to produce more than 2,000 intelligent measurement products, and the annual output value will exceed 10 billion yuan.
Auto Filter Paper
Auto Filter Paper, including Air Filter Paper, oil filter paper, Fuel Filter Paper.
1Good air permeability
2High
efficiency
3High dust holding
4High stiffness and burst resistance
Auto air filters, Auto fuel filters, Auto oil filters, etc.
Our product the automobile pure wood-pulp filter paper in China. Its products mainly include Auto Air Filter Paper, oil filter paper and fuel filter paper. Moreover, the wood pulp we are using is imported from Sweden (NBSK), Chile (Silver-star), USA (HPZ) . we have introduced advanced production technology, imported the equipment from Germany(Voith). We can supply high quality-filter paper.
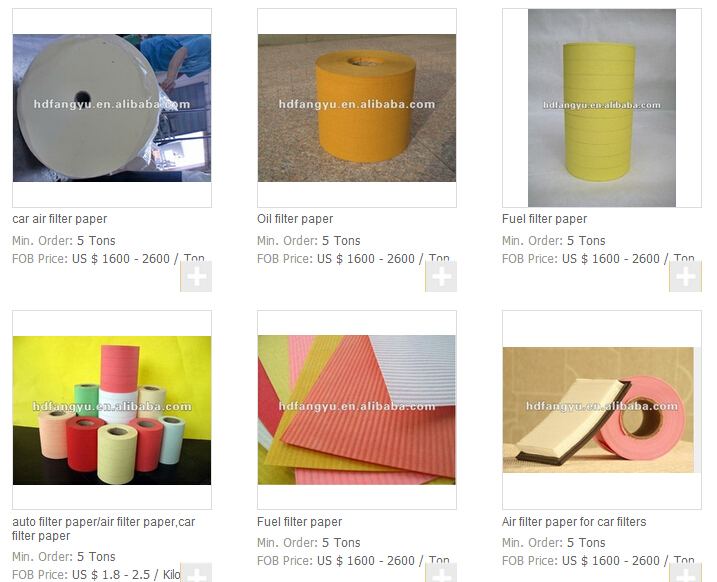
Auto Filter Paper
Auto Filter Paper,Auto Air Filter Paper,Auto Air Cabin Filter Paper,Fuel Filter Paper
Hebei Fangyu Trade Co., Ltd. , https://www.filtersmaterial.com