In recent years, with the rapid development of steel industry and expanding production scale, resulting in the production of iron and steel metallurgy iron-containing ores also will be growing rapidly. It mainly includes sintering dust, blast furnace dust and dust, converter dust, electric furnace dust, rolled steel and dust, etc. These iron ore have relatively high iron content and are a valuable resource for recycling. In addition, metal ore also produces fine ore in the mining process. The re-use of these iron-bearing ore resources is of great significance. Therefore, many pellet plants and steel companies have conducted in-depth research on how to use iron-bearing ore. Research [1-2] .
In the process of using iron ore, there are still the following main problems: 1 The pellets produced are too low in pressure to meet the requirements of the pellets entering the blast furnace smelting. 2 The binder in the preparation process has high requirements on raw materials, and the source of iron ore-containing powder itself is complicated, and strict requirements are impossible. Even some binders require a certain amount of iron containing more than 90% of the raw materials. The metal powder can be solidified, which loses the meaning of using the mineral powder. 3 The curing time of the pellets is too long, and some require several dozen hours of curing time, or dozens of days of curing to produce pressure resistance, and there is no way to achieve mass production.
This research intends to develop a simple, reliable and adaptable pellet production process, and has the advantages of simple equipment, low investment, low production cost and easy operation. To achieve this goal, the drying temperature of the binder must first be Low, the heating time is short, the energy consumption is less, and the environment is not polluted, so a new type of binder was first developed. There have been many studies on binders for pellets [3-6] . On the basis of previous studies, the binders have been further studied and new inorganic and organic binders have been obtained. Based on this, the heating and curing system process was also studied, and the appropriate amount of binder and the adaptability of the binder to different mineral powder materials were explored to obtain iron-bearing ore that could be used in actual industrial production. The pelletization preparation process.
First, test conditions and methods
(1) Raw materials
1. Binder, using homemade inorganic organic composite binder (referred to as binder).
2. Iron-bearing ore, from a certain enterprise in Panzhihua, whose chemical composition is shown in Table 1.
(2) Test process
Each time 500 g of iron-containing ore raw material was weighed, the test was mixed by artificial ingredients, and the sample was pressure-molded on a universal pressure tester. The press molding pressure was 30,000 N/piece, and each pellet was 30 g and the diameter was 25 mm. The powder ore is pressed and formed in a heating furnace for drying and consolidation, and finally its radial resistance is measured. The radial anti-pressure is closer to the force between the two ends of the elliptical pellet produced by the roll briquetting method in actual industrial production, so in the test, the radial anti-pressure of the test specimen used is used. The test process is shown in Figure 1.
(3) Anti-stress test
The sample was a cylinder having a diameter of 25 mm and a height of 20 mm. Five samples were prepared under each condition for stress resistance test, and the highest and lowest values ​​were removed, and the average of the remaining three values ​​was taken as the resistance value under the condition.
(4) Instruments and equipment used
The pressing equipment is YE-30 hydraulic pressure testing machine, the drying equipment is TMF-4-3 ceramic fiber high temperature furnace, and the anti-pressure testing equipment is CMT5105 microcomputer control electronic universal testing machine.
Second, test results and analysis
(1) Effect of heat curing system on pellet pressure resistance
The binder used can be cured under heating conditions, so the heat curing system is one of the important process parameters for pellet preparation. By consulting the literature, the self-made inorganic-organic composite binder was firstly tested by changing the heating and curing temperature under the condition of fixing 12% binder. The test results of the curing temperature on the pellet pressure resistance are shown in the table. 2.
It can be seen from Table 2 that the radial anti-pressure of the sample is changed during the process of changing the heating curing temperature from 300, 400, 500 ° C to 800 ° C by heating the sample directly from room temperature to the heating curing temperature for 1 h. Increasingly, the maximum value is reached at 500 °C. When the temperature is 800 ° C, the radial anti-pressure is reduced. Therefore, a suitable heating temperature of 500 ° C for this process is used. By consulting the literature, when the pellet sample is heated to about 500 ° C, the clay in the pellet sample loses structural water, and the clay becomes dead clay, which is equivalent to the common mud being turned into bricks by firing. The ball is resistant to pressure. Not only that, the conversion of clay to dead clay can make the pellets not disperse under the action of rainwater, but maintain its force, which is conducive to the storage and transportation of pellets after production. This is a large-scale production of pellets. Very important.
During the test, it was found that moisture affected the curing of the binder. Therefore, a process of removing water during heat curing was designed, and the temperature was kept at 105 ° C for 0.5 h to remove the moisture in the sample (Table 3). .
It can be seen from Table 3 that the radial anti-pressure of the pellet sample is significantly improved after 0.5 h incubation at 105 °C. When it is kept at 105 ° C for 0.5 h, the moisture in the pellet sample can be removed, and the moisture is prevented from affecting the curing action of the binder, so the pressure resistance is improved.
In summary, during the heating and curing temperature change from 300,400,500 ° C to 800 ° C, the radial resistance of the sample reaches a maximum at 500 ° C. Therefore, the optimal heating and curing system selected is that the pellets are first raised from room temperature to 105 ° C during the heat curing process, and then heated for 0.5 h, and then continuously heated to 500 ° C and kept for 1 h.
(2) The effect of the amount of binder added on the pressure
In the preparation process of pelletization, the pressure resistance of the pellet is mainly derived from the curing action of the binder, so the amount of binder added directly affects the overall performance of the pellet, and is also in the process of industrial production. The main part of production costs. The test was carried out using the same heat curing process using different binder addition amounts. The test results are shown in Table 4.
As can be seen from Table 4, as the amount of binder added increases, the radial resistance of the pellet sample increases accordingly. When the amount of the binder is 12%, the radial anti-pressure is over the maximum. Continue to increase the amount of binder, when the increase to 14%, the radial resistance is reduced. In the pellet, the radial resistance is mainly generated by the adhesive film formed by the binder during the heat curing process. Therefore, when the amount of the binder is increased, the number of formed adhesive film pellets is correspondingly increased, and the pressure resistance of the pellets is increased. However, when the amount of binder reaches 14%, the amount of binder has already reached saturation state, and more binders can no longer form an adhesive film, which in turn increases the moisture in the pellets and affects the heating of the binder. The curing effect causes its resistance to pressure drop. In the amount of binder added is 12%, first at 105 ° C for 0.5 h, and then continuously heated to 500 ° C and kept for 1 h, in a Panzhihua company to conduct a pilot test, and use the produced The pellets were measured by the drum index and found that most of the drum index was around 67%, and the highest was 90%.
(3) Anti-stress under different powder ore conditions
In order to verify the universality of the pelletization preparation process, three different powder ore materials were selected for testing. 1 raw material 1. High-speed iron powder 36%, medium-added powder 40%, converter sludge 24%, iron content 50.81%. 2 raw materials 2. 20% of mud ore, 30% of medium-added powder, 30% of high-iron powder, 20% of iron concentrate, and 52.31% of iron. 3 raw materials 3. 10% of mud mine, 50% of medium-added powder, 40% of high-iron powder, and 50.89% of iron.
According to the binder addition amount of 12%, the drying system adopts the process scheme of first heating at 105 ° C for 0.5 h, and then continuously heating to 500 ° C and holding for 1 h, and the above three different powder ore raw materials are tested. table 5.
It can be seen from Table 4 that the ratio of the three different raw materials, according to this process, the radial resistance of the pellet sample is at least 1.4153 kN, which meets the requirements for use. The process has no special requirements for powder ore raw materials, has universality, and has a wide application prospect.
Through a test on the influence of the heat curing system and the amount of binder on the spheroidization of iron-containing fine ore, a suitable preparation process was found. The pellets produced by the preparation process have high radial resistance and can meet the requirements of entering the blast furnace smelting; the preparation process has no strict requirements on the raw materials of the iron ore powder, and has universality; in this process, the curing time is About 2h, the production cycle is short, suitable for enterprises to achieve mass production; laid the foundation for solving the main problems existing in the current pellet production.
Third, the conclusion
(1) The experimental research shows that during the heating and solidification process, the pellets are first kept at 105 ° C for 0.5 h, the moisture in the pellets is removed, and the process is continuously heated to 500 ° C and kept for 1 h, and the finished pellets are produced. The radial pressure resistance can be increased from 1.5731 kN to 1.9122 kN. The finished pellets are also resistant to water and are easy to store and transport.
(2) When the amount of binder is 12%, the prepared radial resistance of the pellets reaches 1.9122 kN, which can meet the requirements of blast furnace smelting.
(III) Through the experimental research on different iron-bearing ore mines, it shows that this process has no special requirements for powder ore raw materials and has universal applicability.
references
[1] Gan Qin. Utilization status and development direction of iron dust in Panzhihua Iron and Steel Co., Ltd. [J]. Metal Mine, 2003 (2): 62-64.
[2] Tian Wei, Ma Xiaochun. Process design and application of sintering dust ash mixed steelmaking sludge spraying [J]. Sintered pellets, 2005 (4): 34-36.
[3] Eisele TC, Kawatra S KA review of binders in iron orepelletization [J]. Mineral Processing and Extractive Metallurgy Review, 2003, 24(1): 90-98.
[4] Liu Xinbing, Du Fu. Application of artificial sodiumated bentonite containing organic binder in pellet production [J]. Sintered pellets, 2003, 28 (6): 47-50.
[5] Li Hongwei, Jiang Tao, Qiu Guanzhou, et al. Molecular configuration and selection criteria of iron ore pellet organic binder [J]. Journal of Central South University of Technology, 2000, 31(1): 17-20.
[6] Yang Yongbin. Organic binder replaces bentonite to prepare oxidized pellets [J]. Journal of Central South University: Natural Science Edition, 2007, 38(5): 851-857.
Continuous Waste Tyre Pyrolysis Plant
Pyrolysis Plant is used for recycling waste tire, waste plastic, waste rubber to fuel oil. According to the actual situation in every country and district, we developed different models of Batch Pyrolysis Plants for waste tires, rubber and plastic with daily capacity 25-40 tons.
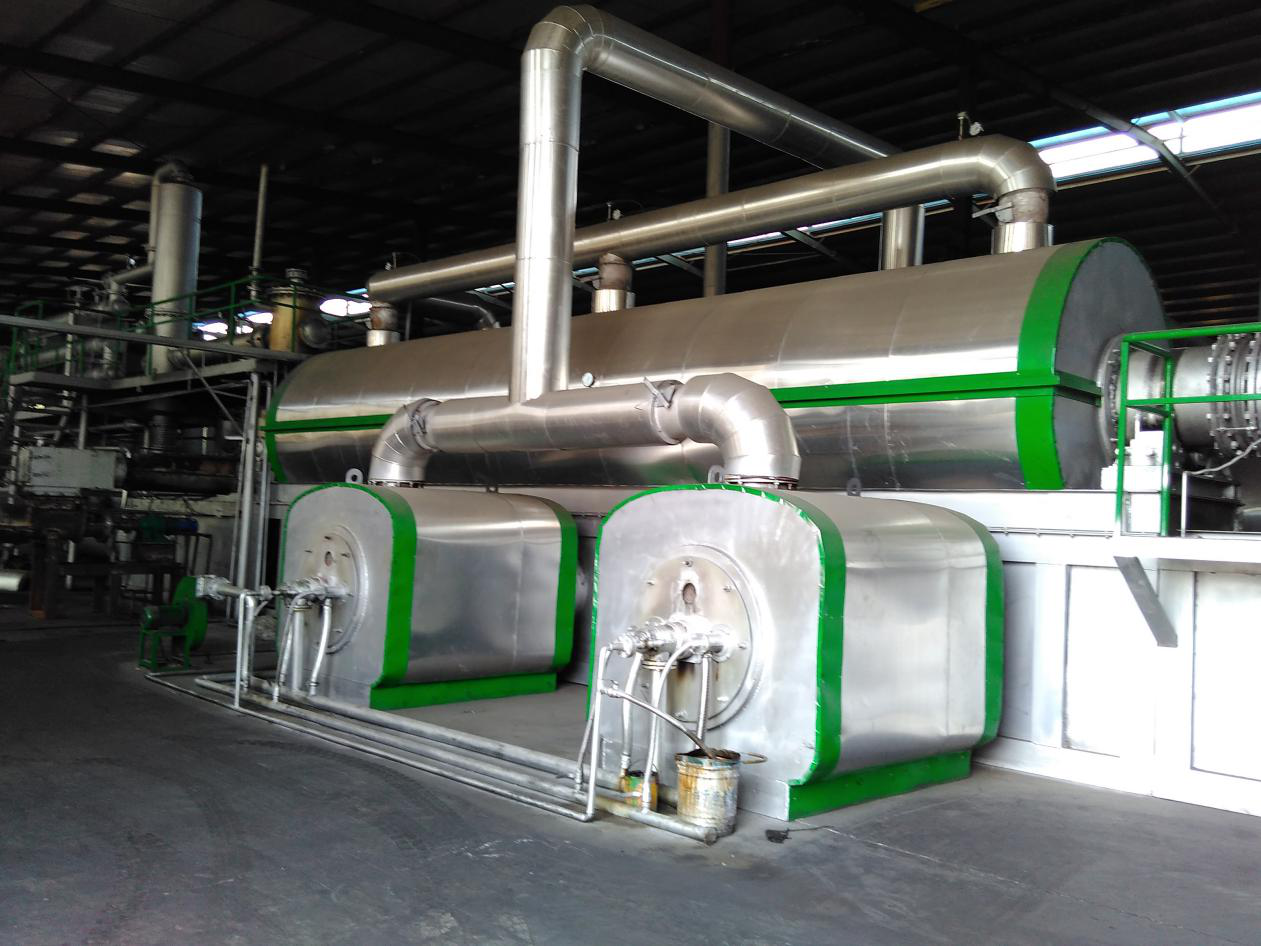
Flowchat of Continuous Waste Tyre Pyrolysis Plant
Advantages of Continuous Waste Tyre Pyrolysis Plant
1. Large daily capacity of 25 MT raw materials, and can work 24 hours without any stop for 15-20 days;
2. Auto-loading, auto-discharging and oil coming out at the same time;
3. Only need fuel for the beginning 2-3 hours, then the sync gas generates itself is enough to support heating, saving fuel cost;
4. Low requirement on the raw materials, no need tiny granule, 5cm pieces acceptable for smooth running;
5. High efficiency condensers, more oil output, good quality oil, easy to clean.
6. Sync gas recycling system, fully burned after recycling and utilization, preventing pollution and saving fuel cost.
7. National patent smoke scrubber, can efficient remove the acid gas and dust of the smoke, environmental friendly to meet related national standards.
8. Easy to operate, need less manpower.
Technical Parameter of Continuous Waste Tyre Pyrolysis Plant
NO. |
ITEM |
Technical Parameter |
1 |
Suitable Raw Materials |
Small pieces of Waste tyre,rubber, waste plastic≤5cm |
2 |
Operating Mode |
Fully Continuous Operation |
3 |
Structure |
Horizontal Type Revolve |
4 |
Loading and discharging |
Fully Automatic Feeding and Discharging under High Temperature at Same Time |
5 |
Capacity(24h) |
8-20Mt |
6 |
Work Pressure |
Slightly Negative Pressure |
7 |
Oil Yield of tyres |
40%-45% |
8 |
Reactor Rotational Speed |
1R/M |
9 |
Installation Power |
110kw |
10 |
Cooling Method |
Cycle water |
11 |
Type of Drive |
Sprocket Wheel |
12 |
Heating Method |
Hot Air |
13 |
Noise dB(A) |
≤85 |
14 |
Main Reactor Weight (MT) |
About 20Mt |
15 |
Total Weight(MT) |
About 45Mt |
16 |
Installation Space Required |
60m*20m |
17 |
Manpower |
2/shift |
18 |
Shipment |
5*40HC |
19 |
Delivery time |
≤70Days |
Continuous Waste Tyre Pyrolysis Plant
Continuous Pyrolysis ,Continuous Pyrolysis Plant,Continuous Waste Tyre Recycling,Waste Tyre To Oil
Shangqiu Jinpeng Industrial Co., Ltd. , https://www.recyclings.nl