Introduction: Three-step engraving machine, as the name suggests, is to do three engraving machines, three heads with cylinder control, can be arbitrarily switched, can easily complete the multi-channel program designed by the customer (the processing of the workpiece requires three in the tool change) This eliminates the cumbersome manual tool change and is suitable for multi-process products in the production of wooden doors, furniture and musical instruments. This unit has a top three units that can catch up with the processing efficiency of three single-head wood engraving machines, one double-head or three independent woodworking engraving machines, and one long woodworking engraving machine.
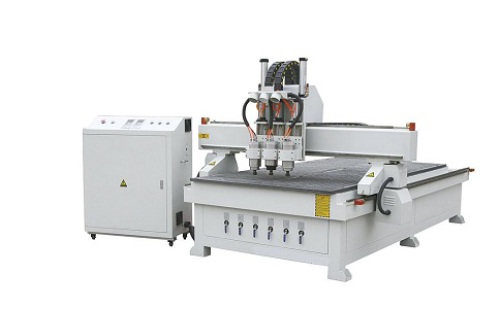
So how does the three-step engraving machine handle the knife?
The CNC engraving machine coordinate system has been determined after leaving the engraving machine. However, the installation position of the workpiece in the machining size range of the machine tool is arbitrary. To determine the position of the workpiece in the coordinate system of the CNC engraving machine, it is necessary to rely on Knife.
Simply put, the tool setting is to tell the CNC machine tool where the workpiece is clamped to the work table. This is done by determining the position of the tool point in the machine coordinate system. The tool-cutting point is the reference point used to determine the position of the workpiece coordinate system in the machine coordinate system after the workpiece is clamped on the machine tool. In order to ensure the correct processing, in the preparation of the program should be reasonable to set the right point.
In general, the tool-cutting point of the CNC engraving machine should be selected at the origin of the workpiece coordinate system. This is conducive to ensuring the accuracy of the tool and reducing the tool-setting error. It is also possible to set the tool-cutting point or the reference point of the tool-cutting tool on the jig positioning element, so that the positioning element can be directly used as the reference tool-setting tool, which is favorable for the accuracy of the position of the workpiece coordinate system during batch processing.
The accuracy of the tool setting will directly affect the machining accuracy. Therefore, the tool setting operation must be careful, and the tool setting method must be compatible with the precision of the part machining. When the precision of parts processing is high, the dial gauge can be used to find the correct tool. With this method, the knife requires a longer time and is less efficient. At present, many CNC Machining centers use new methods such as optical or electronic devices to reduce formulas and improve accuracy.
Forging is a manufacturing process involving the shaping of metal using localized compressive forces. The blows are delivered with a hammer (often a power hammer) or a die. Forging is often classified according to the temperature at which it is performed: cold forging (a type of cold working), warm forging, or hot forging (a type of hot working). For the latter two, the metal is heated, usually in a forge. Forged parts can range in weight from less than a kilogram to hundreds of metric tons. Forging has been done by smiths for millennia; the traditional products were kitchenware, hardware, hand tools, edged weapons, and jewellery. Since the Industrial Revolution, forged parts are widely used in mechanisms and machines wherever a component requires high strength; such forgings usually require further processing (such as machining) to achieve a finished part.
Aluminum Forging Parts are very popular in forging process. We can supply big range of such Aluminum Forging parts.
B. Main particulars
|
MAIN PARTICULARS |
Material for product |
Aluminum |
Standard |
ASTM, ASME, DIN, JIS, ISO, BS, API, EN |
Certificate |
ISO9001, BV |
Dimension |
As per drawing, as large as we can |
Processing |
Forging+blasting+Machining |
Finishing surface |
Machined surface with oil, blasting and painting, anodize, polishing, powder painting, electrophoretic coating- |
Marking |
as per clients` requirements |
Inspection |
material, construction, dimension, heat treatment, hardness, NDT |
Quality |
ISO9001, PPAP control production |
Lead time |
10-30 days for sample, consult with customer for mass production |
Delivery |
Express for sample, ocean shipping/air for mass production |
Our Capabilities |
CNC machining, CNC center machining, drilling, milling, turning, grinding, tapping, boring |
Engineering & manufacturing services |
R&D process, tooling and gauging design, product design Integrated CAD/CAM system, test and measuring |
Others |
Recyclable, in line with environmental requirements and standards, and reliable |
C. Construction
Construction by forging and machining
D Workmanship
The workmanship have good production practice. Care are taken to ensure High accuracy and smooth surfaces
E. Certificates
- Material certificates
- Measuring reports
- Inspection protocol
- NDT reports
- Fixed certificate: ISO9001 certificate
Aluminium forging is performed at a temperature range between 350 and 550 °C
Our service
Besides above the general specifications, we can also supply some specific machining parts as clients' requirements.
Package and shipping
Export cartons, pallets, wooden cases, Polybags
container package and container transportation
Aluminum Forging Parts
Aluminum Forging Parts,Aluminum Forging Parts For Customization,Cnc Aluminum Forging,Aluminum Die Forging Part
Shinvast Industry Ltd , http://www.shinvastindustry.com